Solar energy has become a popular and cost-effective option for many households nowadays. How is it even possible? Well, to understand how solar panels are so efficient and affordable while still providing renewable energy , you have to look at the manufacturing process of solar photovoltaic cells as well as what parts make up a panel. Unveiling this mystery will offer further insight into the amazing power of solar technology!
When it comes to solar panels, consumers have three main choices: monocrystalline, polycrystalline or thin film (“amorphous”) silicon. In this article we’ll take a look at the various ways in which solar cells are constructed and what components go into creating an efficient solar panel. 12v Zener Diode
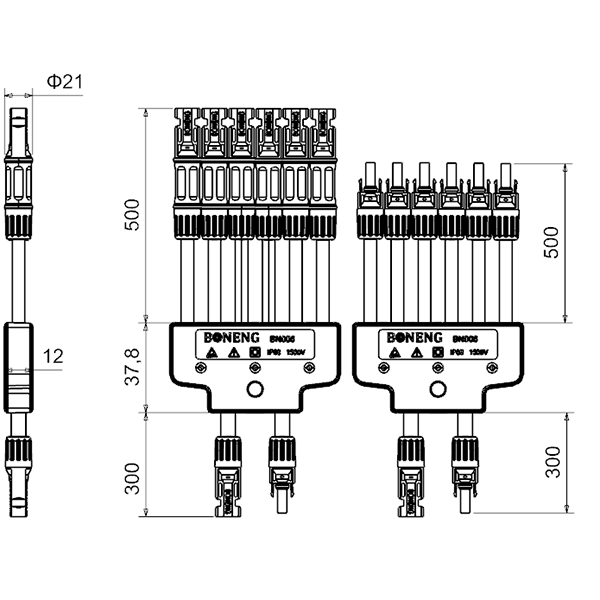
Silicon is a key component in solar panels, acting as the semiconductor that transforms sunlight into usable energy. Without this critical material, many of today’s sustainable energy sources would be impossible. Nevertheless, the materials used to construct the cells are only one component of a solar panel. The production process of solar panels is a captivating journey, where six distinct parts are cleverly combined to build an effective unit. The components of a solar panel include high-grade silicon cells, anodized metal framing, tempered glass sheeting, 12V wiring and bus wire. Do you have a burning interest in the materials of solar panels, and an itch to make one yourself? Then this is for you! Here’s what it takes: familiarize yourself with the most conventional components of a solar panel:
Through the photovoltaic effect, silicon solar cells transform sunlight into electricity by soldering together in a lattice-like arrangement between two glass panels. By responding to the thin wafer sheet of glass, these solar cells generate an electric charge that powers our homes and businesses.
The metal frame of a solar panel serves several invaluable purposes: it guards against the elements, and assists in carefully positioning the device at the desired angle. Not only that, but its reliable construction ensures long-term protection from potentially hazardous circumstances.
Despite its slimness of 6-7 millimeters, the glass casing sheet serves an integral part in shielding the components within – namely, silicon solar cells.
To ensure optimal resilience and protection for the silicon photovoltaic cells, a standard solar panel includes an outer glass casing at its front end. The glass outer layer of the panel is equipped with an insulating casing and a protective back sheet, securely sealing in heat while keeping out humidity. Insulation is a must-have for any solar PV system, as excessive temperatures will lead to an energy inefficiency and ultimately decrease the overall output. To guard against this, manufacturers need to go above and beyond to make sure that light absorption does not come with unnecessary heat exposure.
The 12V wire ensures optimal energy transfer into your inverter, augmenting the sustainability and efficiency of your solar module.
To join multiple solar cells in parallel, bus wires are essential. They come with a thin layer of insulation for simple soldering, and the wire itself is sturdy enough to manage electrical currents efficiently.
By combining monocrystalline and polycrystalline silicon solar cells, soldering them together beneath an anti-reflective glass layer and exposing it to light, a photovoltaic effect is created that produces electricity. There are five distinct steps in the production process of a solar panel:
A solar panel’s most essential elements are its p-type or n-type photovoltaic cells, consisting of crystalline silicon infused with either gallium or boron. The addition of phosphorus allows the cell to carry electrical current. Afterward, a thin sheet is cut from the ingot and covered in an anti-reflective layer before being thinly sliced to facilitate electricity flow through it.
Contrasting p-type and n-type silicon cells lies in their chemical composition. The former is positively charged due to a layer of boron, while the latter are made up of phosphorus, which makes them negative. N-types typically bring more efficiency than p types when dealing with incoming light; yet they wear out quicker under strong sunlight such as we experience during summer months.
Once the silicon wafers obtain their electrical charge from phosphorus, metal connectors are then connected via a process known as soldering. The amount of cells connected at one given time is based on how large the solar panel should be made; 60-cell panels are standard while 72-cells panels may usually be used for commercial projects.
To protect the solar cells, an ultra-durable backsheet made of plastic is installed on their bottom. On top of these cells lies a thin glass sheet that absorbs and filters in sunlight to them. To hold all these components together securely, ethylene vinyl acetate (EVA) glue is used. Finally, they are contained within a metal frame which attaches onto mounting clamps found on your roof for installation.
A junction box is a critical measure to protect your solar panels’ wiring and ensure that electricity continues moving in the right direction. When a panel isn’t producing energy, it can try to absorb power instead – which could lead to dangerous results. That’s why the junction box steps up as guard, preventing any electric current from reversing course so you don’t have an issue with your system running correctly!
Every solar panel brought onto the market must pass a series of tests known as Standard Test Conditions (STC) to guarantee that it will meet all expectations outlined on its technical specification sheet. This entails placing each module in a flash tester and simulating “standard” conditions, such as 1000W/m2 irradiance, 25°C cell temperature and an air mass of 1.5g; if successful then the panel is deemed suitable for shipment and installation.
Solar photovoltaics are composed of a few components, the most essential one being silicon cells. The periodic table’s element number 14, nonmetalic Silicon has electrical conduction properties that convert sunlight into electricity. When light is exposed to a silicon cell, it creates motion in electrons which produces an electric current– this phenomenon is known as “photovoltaic effect.”
However, silicon cells alone cannot provide electricity for your home. To produce usable power, these solar cells must be paired with a metal casing and wiring that enables the electrons to escape from the cell. Silicon is available in numerous different structures, including single-cell (monocrystalline), polycrystalline or amorphous forms; thin film solar panels are generally related to this form of silicon structure.
Monocrystalline solar panels are crafted from one large silicon block and cut into individual wafers, which can then be affixed onto a panel. When compared to their polycrystalline or amorphous counterparts, monocrystalline silicon cells produce more efficient energy. Monocrystalline wafers require a more laborious production process and thus cost more to manufacture compared to their polycrystalline counterparts. With its distinct black aesthetic, many associate this type of cell with the sophisticated look of SunPower’s premium panels.
Polycrystalline solar cells, formed from the fusion of many silicon molecules, are an efficient and cost-effective alternative to monocrystalline cells. Commonly associated with SolarWorld’s blueish hue aesthetic, these silicon cells offer a lower efficiency rate but come at a much more accessible price point.
To conclude, amorphous silicon cells create incredibly bendable solar panel materials that are used in thin film solar panels. Unlike crystalized material, these non-crystalline units attach to a base such as glass, plastic or metal. Given their slim and bendable nature, thin film solar panels are aptly named. Their flexibility makes them an ideal choice for versatility; though not as efficient as mono or polycrystalline cells, these amorphous type of solar cells remain a practical option. U.S.-based First Solar is renowned for producing some of the best thin-film panels in the market today.
After the special solar cell has been crafted, manufacturers complete the process by hooking up its electrical systems, applying an anti-reflective coating to protect it from damage and then enclosing it in a robust glass and metal enclosure.
Find Quality Solar Panel Manufacturers and Installers
If you’re an individual property owner seeking to save money while also reducing your reliance on fossil fuels, the most effective way is to install a home solar photovoltaic system. To find the ideal solution at a competitive price, Solar Marketplace provides free solar quotes from qualified and vetted local installers after signing up. By exploring these offers through their platform, it’s easy to compare important figures such as energy needs met or cost per watt and make an educated decision that best suits you!
Conclusion Solar panels are composed of several components that convert solar energy into usable electricity. The two main elements of any photovoltaic system are a metal frame, typically made from aluminum and glass sheet to protect the cell, along with silicon cells which facilitate the electrical conduction process. Solar panel production involves complex processes such as cutting single-crystalline silicon blocks into individual cells, shaping polycrystalline silicon and attaching amorphous silicon to a base. For quality solar panel systems at a competitive price, explore EnergySage Solar Marketplace for free quotes from reputed installers.
How are solar panels made and how do they work? Solar panels are made up of several components including a metal frame, glass sheet, silicon cells and other electrical components that work together to convert solar energy into electricity. The process of making solar panels involves complex steps such as cutting single-crystalline silicon blocks into individual cells, shaping polycrystalline silicon and attaching amorphous silicon to a base.
What are solar panels made out of? Solar panels are typically composed of two main elements: a metal frame (typically aluminum) and glass sheet to protect the silicon cell. Additionally, they also contain other components such as standard 12V wire, bus wire and connectors. The majority of the panel is made up of silicon solar cells which are responsible for facilitating the electrical conduction process.
Where can I find quality solar panels at a competitive price? EnergySage Solar Marketplace provides free quotes from qualified and vetted local installers after signing up. Through their platform, it’s easy to compare offers and make an educated decision that best suits your needs.
What are the advantages of solar energy? Solar energy has many advantages compared to other traditional sources of energy such as reduced reliance on fossil fuels, cost savings, low maintenance costs and environmental benefits. Additionally, solar energy is abundant, renewable and can be used for a variety of applications.
Jonas Muthoni is an entrepreneur and renewable energy expert. He is the founder of MicroGridMedia.com, a website dedicated to bringing the latest news and information about solar energy and other renewable energy sources to the public. Jonas is passionate about promoting sustainable energy solutions and educating the public about the benefits of renewable energy. He is a regular speaker at industry events and conferences and is committed to driving the transition to a cleaner and more sustainable energy future.
You must be logged in to post a comment.

Solar Connection Box Email address: Leave this field empty if you're human: